2025 Autorius: Howard Calhoun | [email protected]. Paskutinį kartą keistas: 2025-06-01 07:14
Bet kurios įmonės vadovas, nepriklausomai nuo veiklos srities, svajoja, kad augtų pelnas, o gamybos sąnaudos nesikeistų. Tokį rezultatą pasiekti padeda gamyboje esanti „5S“sistema (angliška versija 5S), kuri pagrįsta tik racionaliu vidinių rezervų naudojimu.
Ši sistema nebuvo sukurta nuo nulio. Kažką panašaus XIX amžiaus pabaigoje pasiūlė amerikietis Frederickas Tayloras. Rusijoje tai padarė mokslininkas, revoliucionierius, filosofas ir ideologas A. A. Bogdanovas, išleidęs knygą apie mokslo vadybos principus 1911 m. Jame išdėstytų nuostatų pagrindu SSRS įvedė NOT, tai yra mokslinį darbo organizavimą. Tačiau tobuliausia buvo japonų inžinieriaus Taiichi Ohno pasiūlyta 5C sistema, kurią jis pristatė Toyota Motor gamykloje. Kas tai yra ir kodėl japonų sistema tapo tokia populiari?
Faktas tas, kad jis pagrįstas paprastu principu, kuriam nereikia išlaidų. Jį sudarokitas - kiekvienas darbuotojas, nuo valytojos iki direktoriaus, turėtų kiek įmanoma optimizuoti savo dalį bendroje darbo eigoje. Dėl to didėja visos gamybos pelnas ir didėja visų jos darbuotojų pajamos. Dabar „5C“sistemos įvedimo estafetę perėmė įmonės iš viso pasaulio, įskaitant Rusiją. Šiuo straipsniu bandysime įtikinti skeptikus, kad japonų žinios tikrai veikia ir absoliučiai bet kurioje veiklos srityje.
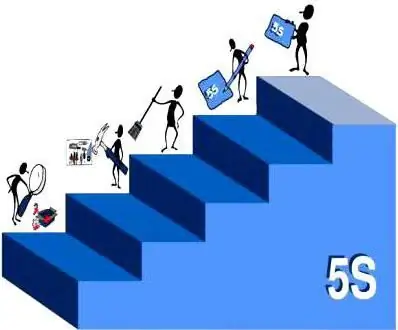
Gamybinė sistema „5C“, kas tai yra
International 5S reiškia penkis žingsnius („žingsnis“angliškai step). Kai kurie ekonomistai ir naujo požiūrio į darbą propaguotojai šį pavadinimą aiškina penkiais japonų postulatais, kurie nuosekliai įgyvendinami 5S sistemoje: seiri, seiton, seiso, seiketsu ir shitsuke. Mums artimesni ir suprantamesni yra gimtieji „5C“- penki iš eilės žingsniai, kuriuos reikia atlikti, kad mūsų produkcija klestėtų. Tai yra:
1. Rūšiuoti.
2. Tvarkos palaikymas.
3. Švaros palaikymas.
4. Standartizavimas.
5. Tobulinimas.
Kaip matote, „5C“sistemai gaminti nereikia nieko antgamtiško. Galbūt todėl vis dar galima sutikti nepasitikėjimą ir lengvabūdišką požiūrį į ją.
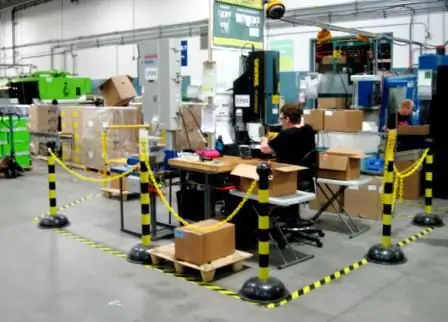
Sistemos kūrimo etapai
Išmintingas japonas Taiichi Ohno, kuris, įdiegęs savo metodus Toyota gamykloje, sugebėjo pakilti išinžinierius generaliniam direktoriui, pastebėjo, kiek daug nuostolių atsiranda dėl įvairių neatitikimų ir perdangų. Pavyzdžiui, kai kurie smulkūs varžteliai nebuvo laiku uždėti ant konvejerio ir dėl to nutrūko visa gamyba. Arba atvirkščiai, detalės buvo tiekiamos su marža, jos pasirodė perteklinės ir dėl to vienas iš darbuotojų jas turėjo vežti atgal į sandėlį, vadinasi, gaištamas laikas tuščiam darbui. Taiichi Ohno sukūrė koncepciją, kurią pavadino „laiku“. Tai reiškia, kad dabar į konvejerį buvo pristatyta lygiai tiek dalių, kiek reikia.
Galima pateikti kitų pavyzdžių. Gaminama sistema „5S“taip pat apėmė „kanban“sąvoką, kuri japonų kalba reiškia „reklaminis ženklas“. Taiichi Ohno pasiūlė prie kiekvienos detalės ar kiekvieno įrankio pritvirtinti vadinamąją „kanban“etiketę, kurioje buvo pateikta visa reikalinga informacija apie detalę ar įrankį. Iš esmės tai taikoma bet kam. Pavyzdžiui, į prekes, vaistus, aplankus biure. Trečioji koncepcija, kuria remiasi 5S sistema gamyboje, yra „kaizen“koncepcija, kuri reiškia nuolatinį tobulėjimą. Buvo sumanytos ir kitos koncepcijos, kurios tiko tik labai specializuotiems gamybos procesams. Šiame straipsnyje mes jų nenagrinėsime. Dėl visų praktikoje išbandytų naujovių suformuoti 5 žingsniai, kurie pritaikomi bet kokiai gamybai. Išanalizuokime juos išsamiai.
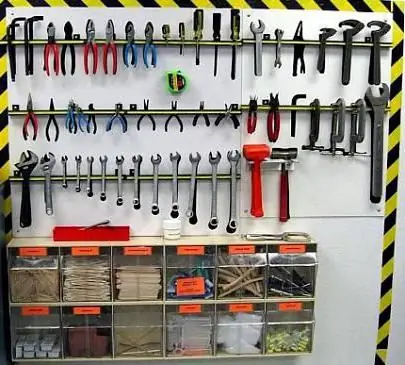
Rūšiavimas
Daugelio iš mūsų staliniuose kompiuteriuose yra elementų, kuriuose yraiš esmės nereikia. Pavyzdžiui, senos formos, nenaudojamos bylos, skaičiavimų juodraščiai, servetėlė, ant kurios buvo kavos puodelis. Ir tarp šio chaoso gali būti reikalingų bylų ar dokumentų. Pagrindiniai „5S“sistemos principai - optimizuoti savo darbo eigą, tai yra užtikrinti, kad laikas nebūtų švaistomas ieškant tinkamų dalykų tarp nereikalingų griuvėsių. Tai yra rūšiavimas. Tai yra, darbo vietoje (prie mašinos, ant stalo, dirbtuvėse - bet kur) visi daiktai yra išdėlioti į dvi krūvas - būtini ir nereikalingi, kuriuos reikia išmesti. Be to, viskas, ko jums reikia, yra suskaidoma į šias krūvas: „naudojama dažnai ir nuolat“, „naudojama retai“, „beveik nenaudota“. Tai užbaigia rūšiavimą.
Tvarkos laikymasis
Jei tik išardysite elementus, nebus jokios prasmės. Šiuos daiktus (įrankius, dokumentus) būtina sutvarkyti taip, kad nuolat ir dažnai naudojamasi būtų matomi arba kad būtų galima greitai paimti ir lengvai padėti atgal. Tai, kas retai naudojama, gali būti siunčiama kur nors dėžutėje, tačiau prie jos turi būti pritvirtinta kanban etiketė, kad po kurio laiko būtų galima lengvai ir tiksliai rasti. Kaip matote, 5S sistema darbo vietoje prasideda nuo pačių paprasčiausių žingsnių, tačiau iš tikrųjų ji pasirodo labai efektyvi. Be to, tai pagerina nuotaiką ir norą dirbti.
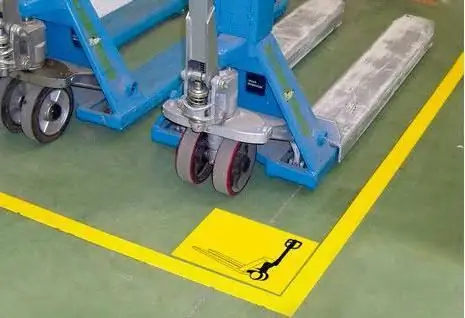
Švaros palaikymas
Šis trečiasis žingsnis daugeliui yra logiškiausias. Nuo vaikystės esame mokomi būti švarūs. Antgamyboje taip pat būtina, o ne tik biuro darbuotojų stalai ar kabinetai maitinimo įstaigose, bet ir mašinos, valytojų ūkinės patalpos turėtų būti švarūs. Japonijoje darbuotojai gerai prižiūri savo darbo vietas, jos valomos tris kartus per dieną - ryte prieš darbą, pietų metu ir vakare, darbo dienos pabaigoje. Be to, jų įmonėse įdiegtas specialus zonų žymėjimas, leidžiantis laikytis tvarkos gamyboje, tai yra skirtingomis spalvomis žymimos gatavų gaminių plotai, tam tikrų dalių sandėliavimas ir pan.
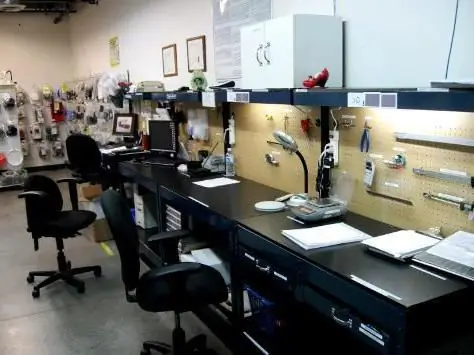
Standartizacija
Standartizacijos principus išrado Taiichi Ohno. Juos taip pat plačiai naudoja šiuolaikinė 5S sistema. Gamybos valdymas standartizacijos dėka gauna nuostabų įrankį visų procesų valdymui. Dėl to greitai pašalinamos grafiko vėlavimo priežastys ir ištaisomos klaidos, dėl kurių išleidžiami žemos kokybės produktai. „Toyota Motor“gamykloje standartizavimas atrodė taip: meistrai sudarė dienos darbų planus, darbo vietoje buvo iškabintos tikslios instrukcijos, o darbo dienos pabaigoje specialūs darbuotojai patikrino, kokie nukrypimai nuo plano įvyko per dieną ir kodėl. Tai yra pagrindinė standartizacijos taisyklė, tai yra tikslios instrukcijos, darbo planai ir jų įgyvendinimo kontrolė. Dabar daugelis įmonių, pavyzdžiui, ENSTO gamyklos Estijoje, diegia premijų sistemą darbuotojams, kurie griežtai laikosi 5C sistemos nuostatų ir tuo remdamiesi didina savo darbo našumą,yra puiki paskata priimti šią sistemą kaip gyvenimo būdą.
Tobulinimas
Penktasis žingsnis, užbaigiantis „5S“sistemą gamyboje, yra pagrįstas kaizen koncepcija. Tai reiškia, kad visi darbuotojai, nepaisant užimamų pareigų, turėtų stengtis tobulinti darbo procesą jiems patikėtoje srityje. Kaizen filosofinė esmė ta, kad visas mūsų gyvenimas kasdien gerėja, o kadangi darbas yra gyvenimo dalis, jis taip pat neturėtų likti nuošalyje nuo tobulėjimo.
Veiklos laukas čia platus, nes tobulumui ribų nėra. Pagal japonų sampratą, patys darbuotojai turi norėti tobulinti savo gamybos procesą, be nurodymų ar prievartos. Dabar daugelis organizacijų kuria darbuotojų komandas, kurios stebi produktų kokybę, moko kitus apie savo teigiamą patirtį ir padeda siekti tobulumo.
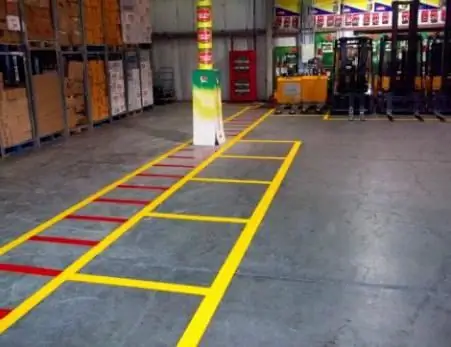
Pagrindinės klaidos
Kad „5C“sistema pradėtų veikti, neužtenka ją suorganizuoti ar samdyti darbuotojus, kurie privers ją diegti kolegas. Svarbu, kad žmonės suvoktų šios naujovės naudingumą ir priimtų ją kaip gyvenimo būdą. „5S“sistemos įdiegimas Rusijoje gamyboje susiduria su sunkumais būtent todėl, kad mūsų rusiškas mentalitetas skiriasi nuo japoniško. Daugeliui mūsų kūrinių būdingi šie požymiai:
1. Darbuotojai, ypač jei jiems nėra paskatų, nesiekia didinti įmonės pelno. Jie klausia,kam stengtis, kad viršininkas būtų dar turtingesnis, jei jis jau viską turi.
2. Patys vadovai nesidomi „5S“sistemos įvedimu, nes nemato joje tikslingumo.
3. Daugelis direktyvų „žemyn iš viršaus“yra įpratusios vykdyti tik „varnelei“. Japonijoje yra visiškai kitoks požiūris į jų darbą. Pavyzdžiui, tas pats Taiichi Ohno, pristatydamas „5S“sistemą, galvojo ne apie asmeninę naudą, o apie įmonės, kurioje jis buvo tik inžinierius, naudą.
4. Daugelyje įmonių 5S sistema įvedama priverstinai. Liesi gamyba, reiškianti visų rūšių nuostolių (darbo laiko, žaliavų, gerų darbuotojų, motyvacijos ir kitų rodiklių) eliminavimą, neveikia, nes darbuotojai pradeda priešintis naujovėms pasąmonės lygmenyje, o tai galiausiai sumažina visas pastangas iki nulio..
5. Sistemą diegiantys vadovai nevisiškai supranta jos esmę, o tai sukelia nusistovėjusių gamybos procesų gedimus.
6. Standartizacija dažnai perauga į biurokratiją, geras poelgis apauga instrukcijomis ir nurodymais, kurie tik trukdo dirbti.
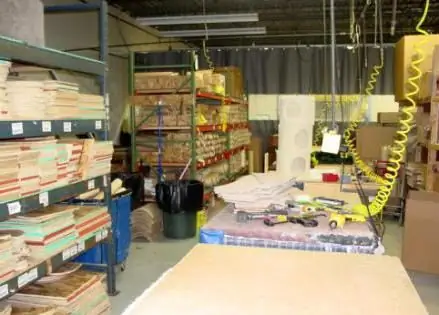
Apžvalgos
Rusų, kurie gamyboje pristatė „5S“sistemą, atsiliepimai apie šią naujovę labai dviprasmiški. Paryškinti privalumai:
- geriau būti darbo vietoje;
- neaiškite dėmesio nuo darbo nereikalingomis smulkmenomis;
- aiškesnė darbo eiga;
- pamainos pabaigoje sumažėjo nuovargis;
- šiek tiek padidėjoatlyginimas didinant darbo našumą;
- sužalojimų darbe sumažėjo.
Pažymėti trūkumai:
- rūšiuodami priverčia viską išmesti;
- standartizacija padidino biurokratiją;
- „5C“sistemos įdiegimas nepadidina problemų visose įmonės srityse;
- 5S sistemos iškėlimas į pirmą vietą užgožė tokias svarbias problemas, kaip atsarginių dalių trūkumas.
Rekomenduojamas:
Sistema „Rapida“: aprašymas, funkcijos ir apžvalgos
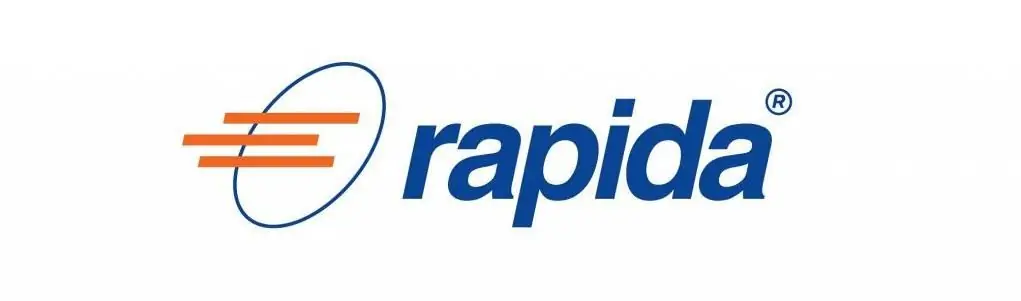
Mokėjimo sistema „Rapida“yra universali paslauga. Jos paslaugos tinka tiek paprastiems vartotojams, tiek verslo savininkams. Apsvarstykite platformos ypatybes ir tai, kaip vyksta klientų registravimo ir identifikavimo procedūra
Centralizuotas valdymas: sistema, struktūra ir funkcijos. Valdymo modelio principai, sistemos privalumai ir trūkumai
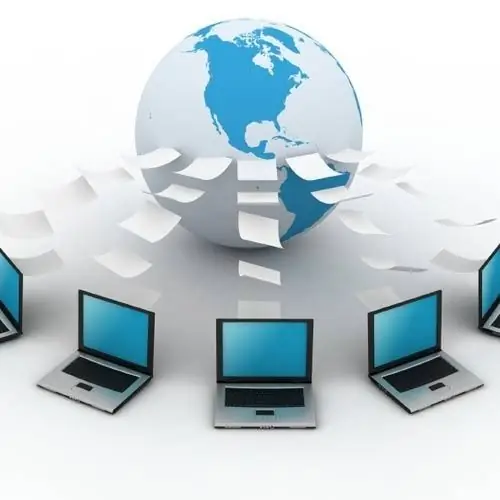
Kuris valdymo modelis geresnis – centralizuotas ar decentralizuotas? Jei kas nors atsakydamas nurodo į vieną iš jų, jis menkai išmano valdymą. Nes vadyboje nėra blogų ir gerų modelių. Viskas priklauso nuo konteksto ir jo kompetentingos analizės, leidžiančios pasirinkti geriausią būdą valdyti įmonę čia ir dabar. Centralizuotas valdymas yra puikus to pavyzdys
Viešbučio valdymo sistema: geriausių programų apžvalga, funkcijos, aprašymas, apžvalgos
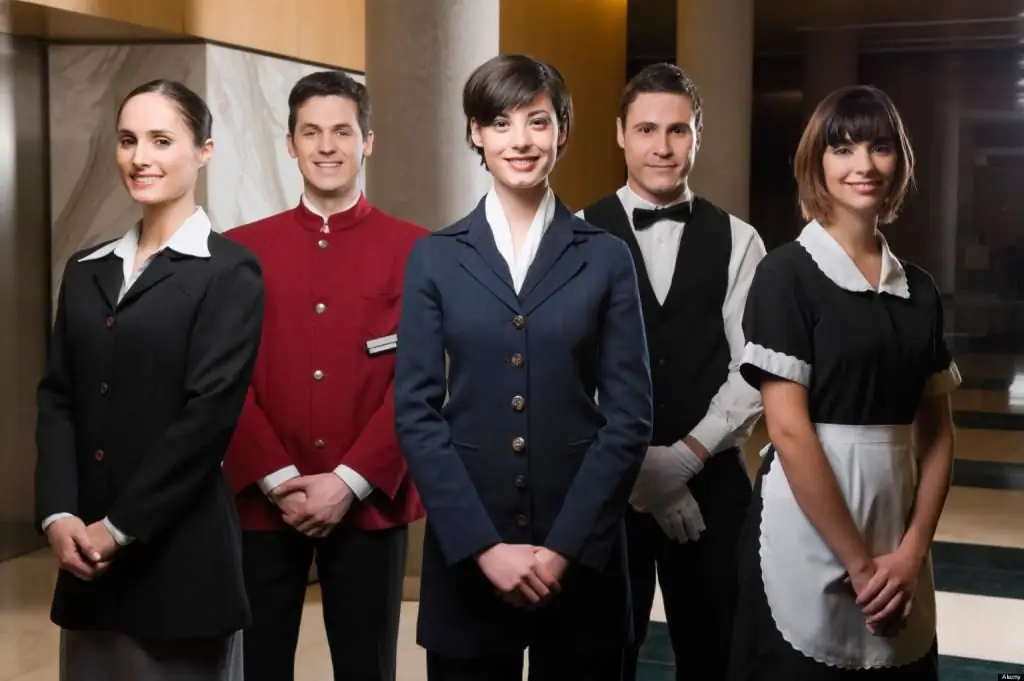
Viešbučio valdymo sistema padės tinkamai organizuoti įstaigos dokumentacijos priežiūrą, pašalinti klaidas. Geriausių programų ir jų galimybių aprašymas. Kaip pasirinkti programą, atsižvelgiant į jūsų viešbučio ypatybes
Logistikos centrai yra Aprašymas, funkcijos, užduotys ir funkcijos
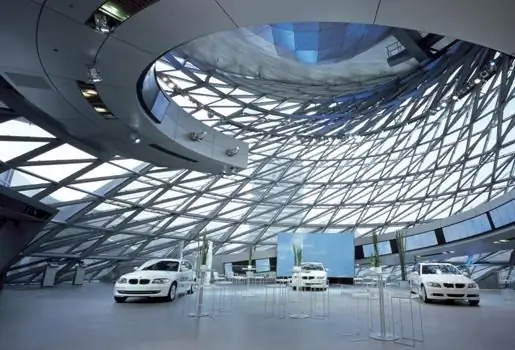
Logistikos centrai – tai įmonės, kurios apdoroja ir sandėliuoja prekes, o prireikus atlieka ir muitinės formalumus. Be to, jie gali teikti informacines paslaugas, taip pat pasiūlyti universalius krovinių vežimo sprendimus. Tokie centrai turi daug funkcijų, kurios bus aptartos toliau
"Kanban", gamybos sistema: aprašymas, esmė, funkcijos ir apžvalgos
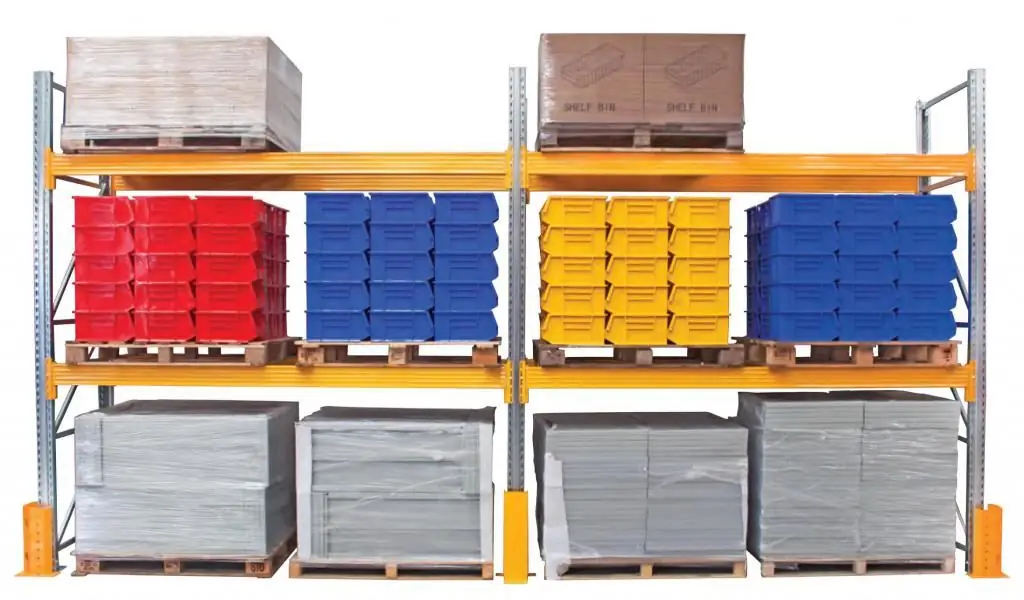
Kanban yra labiausiai žinomas pramoninės gamybos valdymo metodas pagal „Just-in-Time“koncepciją. Esant minimalioms organizacijos išlaidoms, galima žymiai sumažinti darbo laiką ir materialinių išteklių sąnaudas